用于机床制造和特种机械制造的即插即用直线系统
发布时间:2016-07-22 10:25:51 阅读次数:1203
用于机床制造和特种机械制造的即插即用直线系统
通过功能整合获得经济的解决方案
舍弗勒工程师在公司自主研发的铝挤压型材中集成了直线导轨、齿形带传动和滚珠丝杠传动、行星齿轮箱、测量系统、旋转编码器、承载滑块、润滑系统、限位开关和盖板等。 除标准部件之外,舍弗勒还为客户研发和制造了量身定制的个性化直线系统。 根据各自的负载情况用FEM对其进行优化。用直接驱动、伺服电机、控制器和传感器等产品系列研发和制造的直线系统也有完备的电气功能。舍弗勒将广泛的滚动轴承和直线轴承产品系列与滚动轴承专业知识相结合,诞生出高集成度的创新解决方案。
可伸缩直线执行器MTKUSE:为机床赢得更多空间
与标准直线轴相比,伸缩轴的巨大优势是不会延伸到整个运行路径,因此可为其他机器和工序释放工作空间。将可伸缩直线执行器作为辅助轴使用,可以为机床设计提供更多的设计选项。在防护墙后的区域或不同的工作区域传输工件也是可行的。
舍弗勒直线技术部专为此类辅助轴,例如拾放应用或刀具交换,研发了可伸缩直线执行器MTKUSE。其中3个精密直线循环球轴承及导轨组件上下叠放,使可能的运行路径长度达到了原本直线执行器的两倍多。直线单元可往两个方向伸缩。伺服电机安装在铝型材外部,并通过齿轮齿条传动装置来驱动直线执行器。根据客户要求,可安装不同制造商的伺服电机和与之相配的小间隙精密行星齿轮箱。也可根据客户要求集成限位开关和位移测量系统。通过伺服控制器可进行电流检测和位置误差监控,间接评估摩擦力矩及轴承状态。
高精度直线工作台LTP:高精度和高重复定位精度的运动
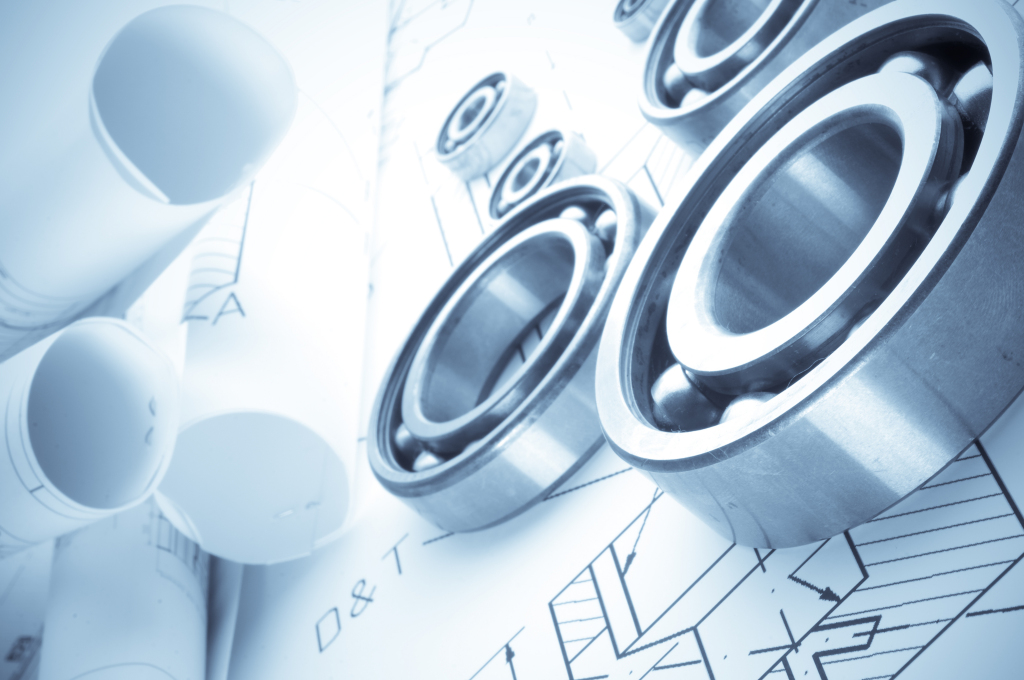
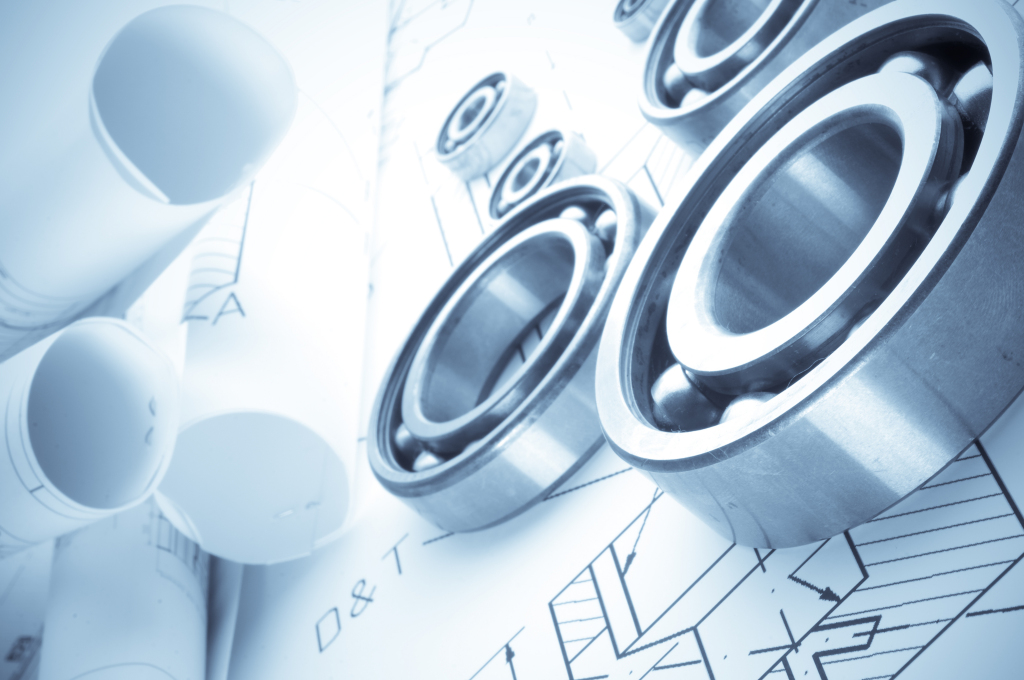
如果加工或检验时需要高精度和极高的重复定位精度移动工具,就需用到高精度直线工作台LTP。 直线滑台通过安装在高精度制造铝板上的精密直线循环球轴承及导轨组件进行支撑和导向。直线循环球轴承及导轨组件使LTP工作台能平稳地低噪音,低阻力运行。它通过伺服电机和滚珠丝杠驱动,也可替换成直接驱动的版本。根据客户要求可以增加位移测量系统和位置开关。高精度直线工作台LTP有三种尺寸,还可选择减振灰铸铁材质。为了防止异物和液体进入,可为LTP配备风琴式密封罩或金属伸缩密封罩。为了能根据客户要求安装不同制造商的伺服电机,联轴器座KGEH被改造为开放的接口。 LTP也可通过伺服控制器间接评估摩擦力矩及轴承或丝杠状态。高精度直线工作台可用作机床上的辅助轴,用于刀具交换,或作为激光打标设备的进给轴。
舍弗勒已开发出用于集成轴系行程检查的测量系统系列LMSA(Length Measuring System – Analog,长度测量系统 – 模拟)。它基于电感的模拟测量原理,可实现的测量精度为+ / - 3um/m。该系统的特点是坚固耐用,对磁干扰不敏感,并且无滞后现象。传感器头直接安装在滑块的刚性鞍板上。利用高频交变的磁场扫描导轨头部增量尺寸,并产生具有90°相位偏移的两路传感器信号。一根高精度蚀刻的测量钢带构成了测量尺。测量头与测量钢带之间的距离在制造过程中被精确设置,但如需要调整,可通过四个固定螺钉重置。传感器头和测量钢带之间的运动使各线圈互感,因此产生了正弦波信号。也就是说LMSA测量系统具有1Vss的模拟输出信号,其高倍细分信号周期为 10µm。因此,该测量系统可以方便地与现有控制系统进行结合。
用于质量和生产流程可靠性检测的诊断系统
计划内停机期间基于实际使用情况的部件替换,始终如一的高加工品质,降低生产损失导致的成本——所有这些对于当今现代机床的使用者和制造商都非常重要。作为部件和状态监控系统的制造商,舍弗勒工业后市场业务部通过其经证实的产品和极具价值的专家服务成为行业中一个可靠的合作伙伴。有多种轴承诊断系统可满足要求并服务于特定的监控方案,例如FAG Detector III、 FAG DTECT X1 s以及FAG ProCheck。舍弗勒在应用于机床中的FAG SmartCheck中安装了一款创新的在线系统,它能够提供关于机床部件状态的全面信息,同时将额外的参数考虑进去。使用FAG SmartCheck可以分三个扩展阶段对机床进行监控。在第一阶段中,单个部件以分散的方式进行监控,这样可以依照数据直接访问设备。根据测量数据,FAG SmartCheck确定合理的警戒点。一款SmartCheck应用程序确保了可通过智能手机存取数据。如果使用者选择第二阶段,仪器会智能地集成到机床的控制系统中。过程整合可通过通信接口实现。第三阶段使服务范围得以扩大。其中可能包括通过网络连接进行远程存取,或者甚至是咨询或其他服务。将FAG SmartCheck与控制系统进行过程集成可通过采用由适用的输入和输出提供的通信选择进行。这为使用界面方式与机器进行交流提供了一种可能性和基础——其同样适用于工业4.0(Industrial 4.0)背景下——并意味着未来机器可具备诸如自我诊断的功能。此外,根据客户的要求,还可以使用一系列附加的监控系统。
上一篇:胶印机五大自动控制装置介绍